Activity
The Ukiyo-e (Woodblock) Printing Process
Woodblock printmaking was a complex process involving the collaboration of several people: publisher, artist, carver, and printer.
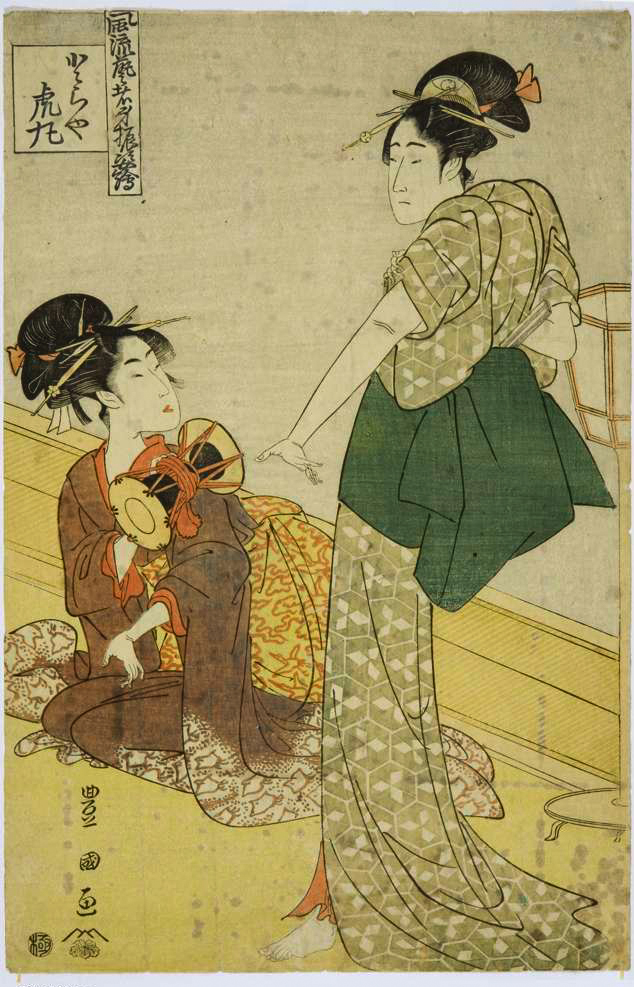
A Geisha Performing as Toraya Toramaru (Toraya Toramaru) from An Almanac of Geisha Imitating Famous Actors (Furyu Geisha Miburi Sugata-e). By Utagawa Toyokuni (1769-1825). Ink and colors on paper. Gift of the Grabhorn Ukiyo-e Collection, 2005.100.100.
A Geisha Performing as Toraya Toramaru (Toraya Toramaru) from An Almanac of Geisha Imitating Famous Actors (Furyu Geisha Miburi Sugata-e). By Utagawa Toyokuni (1769-1825). Ink and colors on paper. Gift of the Grabhorn Ukiyo-e Collection, 2005.100.100.
Ukiyo-e (literally “pictures of the floating world”) is the name given to paintings and prints primarily depicting the transitory world of the Yoshiwara—the licensed pleasure quarter and center of social life in the city of Edo (present-day Tokyo) during the Edo period (1615–1868) in Japan. It is a composite term of uki (floating), yo (world), and e (pictures). Originally, ukiyo was a Buddhist term to express the impermanence of human life. During the Edo period, however, ukiyo came to refer to the sensual and hedonistic pleasures of people, who embraced them all the more for their ever-changing nature.
In order that ukiyo-e prints feature the latest favorites of a discerning public, prints had to be published very quickly. Publication was a complex process involving the collaboration of several people: publisher, artist, carver, and printer. Publishers were the key figures in the printing process from start to finish: assessing the market, hiring the designer, supervising production, and arranging for distribution. It was the publisher’s seal that appeared on each print, with the artist’s signature. The only other person who had a say in production was the government censor, who checked all designs to make sure they were neither immoral nor politically subversive.
After a publisher had decided upon the subject matter for a print or series of prints, he commissioned an artist to create the design. The artist would draw his composition in black ink on a thin sheet of paper. Although the artist might include notes and directions on his drawing, he was not involved in the printing process. This could sometimes lead to the artist’s dissatisfaction with the finished product, due to unexpected changes made by the printer or engraver.
The artist’s drawing was then sent to the printer’s workshop, where it was pasted face down on a block of smooth cherrywood. Oil was sometimes applied to the paper to make the outlines more visible. The paper was then pulled away (Japanese paper was very strong and fibrous) to leave a thin layer behind with the design outlines showing through.
The engraver then cut away all the wood around the lines, a crucial task requiring great skill. The beauty and refinement of Japanese woodblock prints was dependent on his fine touch. After the block face had been carved, printers removed the residue of paper and carefully brushed black sumi ink onto the raised lines of the block. They placed the damp paper to be printed on the block, and rubbed it rigorously with a baren, a tool made of twisted cord covered with a bamboo sheath. This rubbing motion forced the paper into hard contact with the inked lines of the wood block. These line proofs were then given to the government censor for approval and to the artist for coloring. Using the artist’s hand-colored proof, the engraver would cut more blocks, one for each color and each with registration marks (kento) to assure that the lines and colors would be in proper alignment on each pass.
Now everything was ready for the final printing and distribution. Several printers would ink and press the paper onto each of the blocks. Colors were printed one at a time; a minimum of about ten impressions were necessary to print an average nishiki-e. With each impression, printers had to align the paper into the registration marks in the block, so that colors with each successive pass would fall in the proper location. Paper came in three typical sizes: chuban (literally “medium block” measuring about 10.5 x 7.5 in), aiban (“medium-large block” measuring about 13 x 9 in), and oban (“large block” measuring 10.5 x 15.5 in). Oban was the standard size used for ukiyo-e.
About 200 prints (the usual edition of any particular design) could be made in one day. Sometimes, blocks kept in storage would be reprinted, but as the wood wore down, the line quality gradually deteriorated. However, as many as 8,000 prints could be made from a block before cutting a new one. The soft, water-soluble colors, which were until the late nineteenth century derived from plant and mineral sources, were applied in relatively large flat areas bordered by the fine line drawing of the design. Even when artists borrowed shading techniques from the West, the woodblock process still created an essentially flat image, one of the special characteristics of Japanese prints.